Dongguan 2025/3/26 – In an era where fast fashion dominates consumer trends, understanding how clothing is made has never been more critical. This week, we visited Auschalink in China to explore the intricate process behind transforming raw materials into the garments hanging in your closet.
1. Design & Prototyping
The journey begins in the design studio. Teams of designers and pattern-makers collaborate to create sketches and digital models using CAD (Computer-Aided Design) software. Once a design is finalized, a physical prototype is stitched and tested for fit, comfort, and aesthetics. "Sustainability is now a priority," says lead designer Kanina. "We optimize patterns to minimize fabric waste from the start."
2. Fabric Sourcing & Preparation
Factories source materials ranging from organic cotton to synthetic blends, often partnering with global suppliers. Upon arrival, fabrics undergo rigorous quality checks for color consistency, durability, and shrinkage. Pre-treatment processes like washing or dyeing ensure materials meet exact standards before cutting.
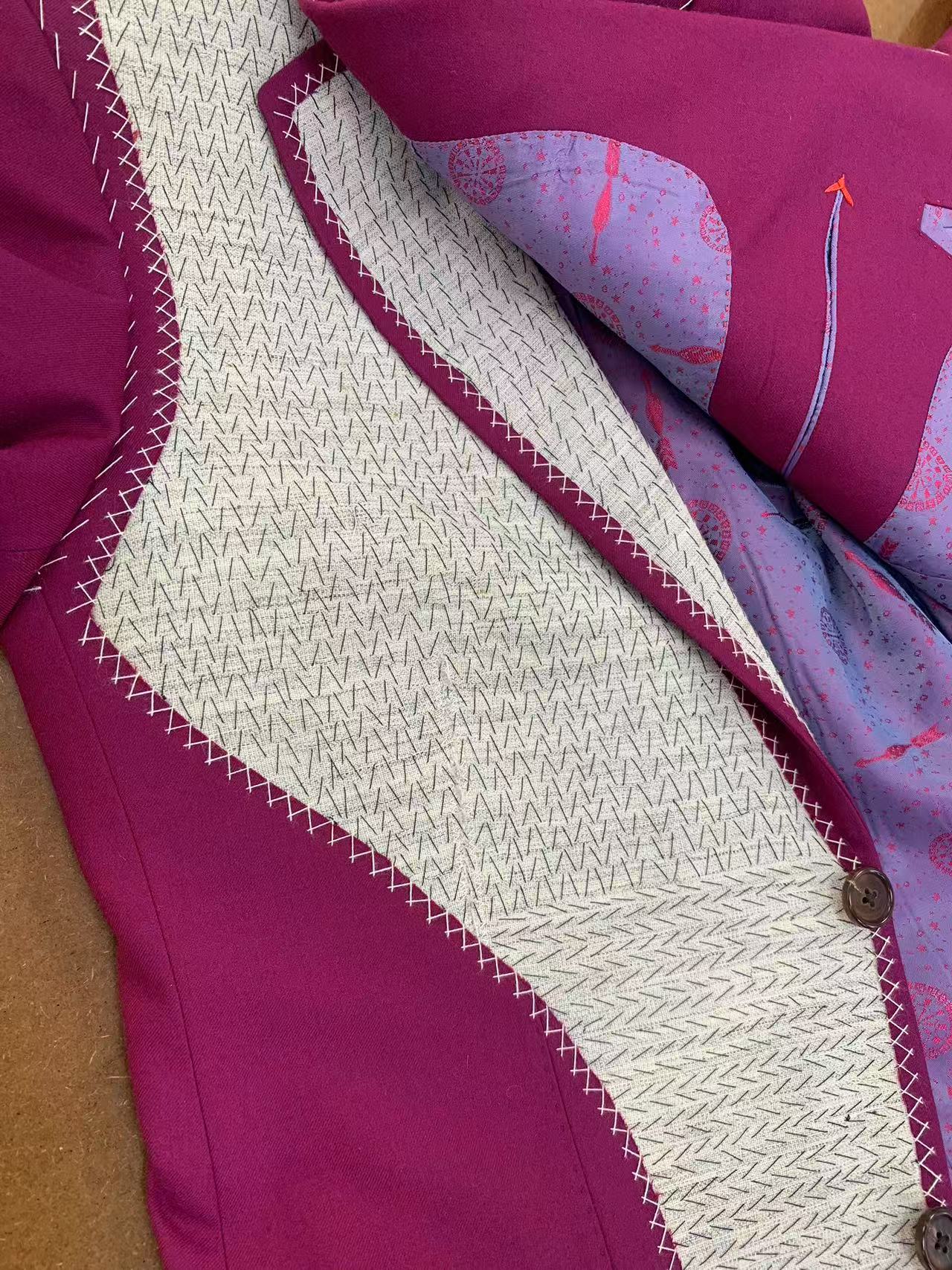
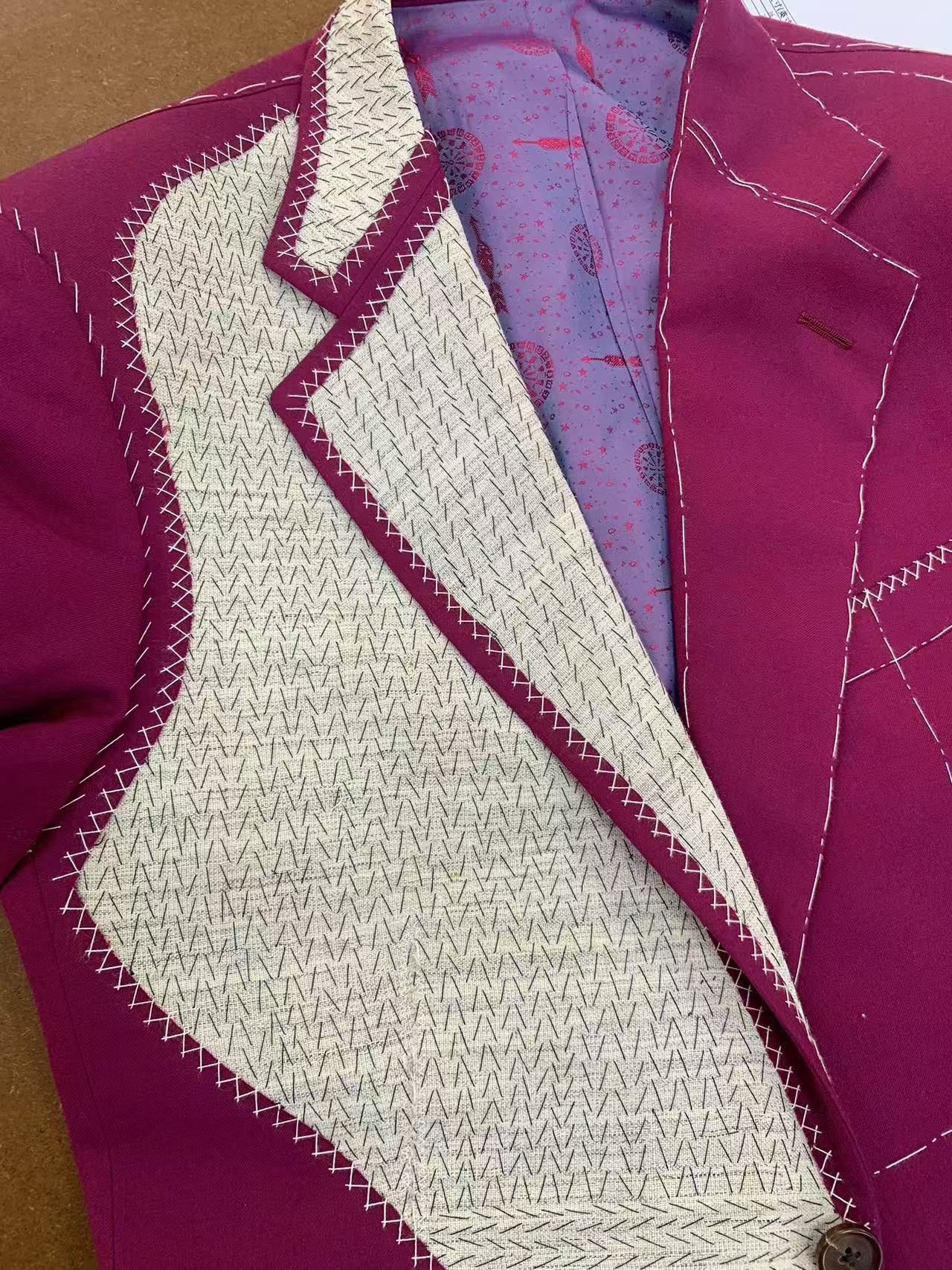
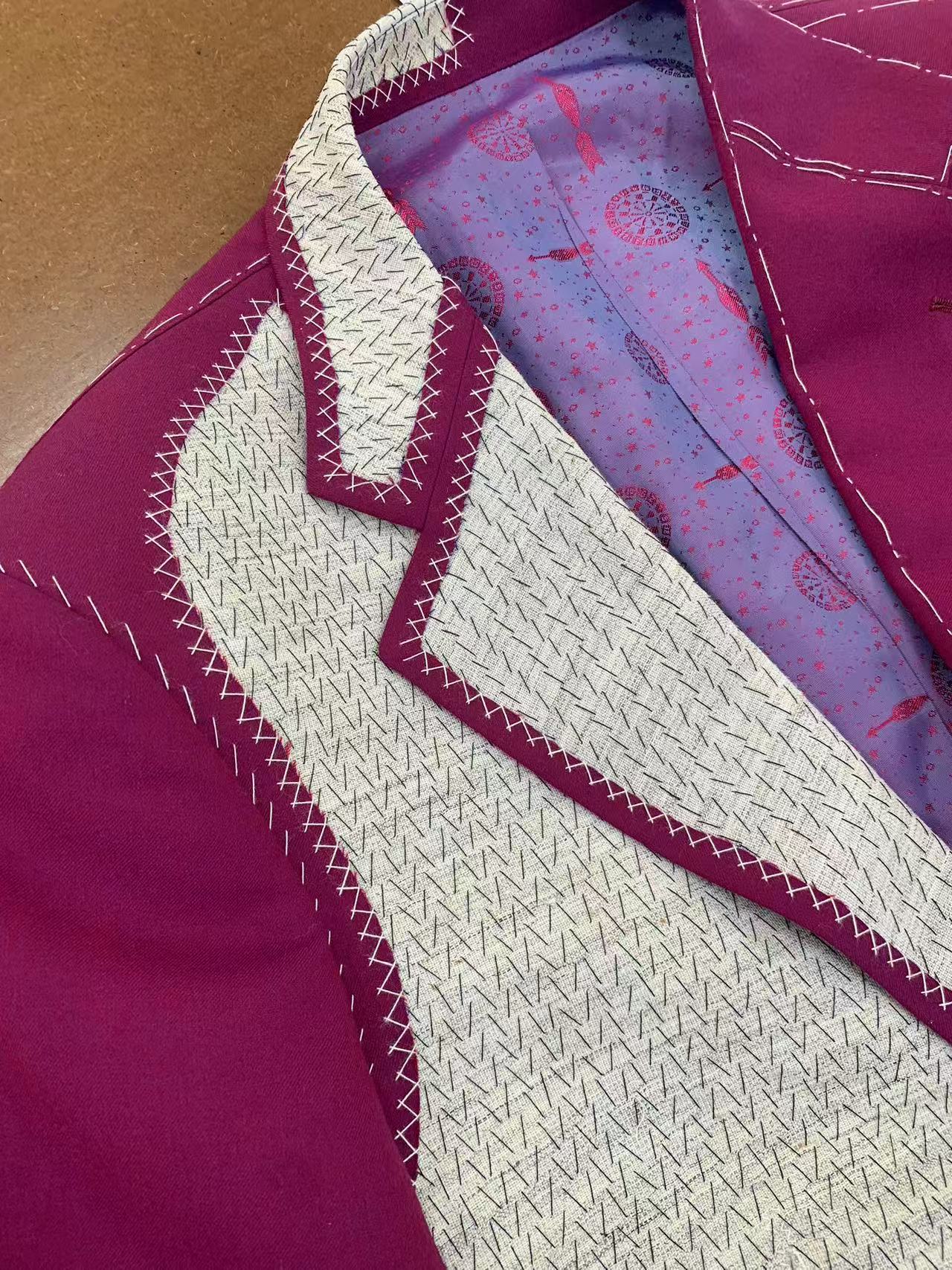
3. Automated Cutting
In the cutting room, layers of fabric are spread onto long tables. Computer-controlled cutting machines, guided by digital patterns, slice through the material with precision. "Automation reduces errors by 30% compared to manual cutting," explains production manager Jenny. Leftover fabric scraps are recycled into insulation or recycled textiles.
4. Assembly Line Sewing
Cut pieces move to sewing stations, where skilled workers operate specialized machines. Collars, sleeves, and seams are meticulously stitched in sequence. Larger factories use modular systems—teams focus on specific garment sections to boost efficiency. Quality inspectors spot-check seams and stitching at every stage.
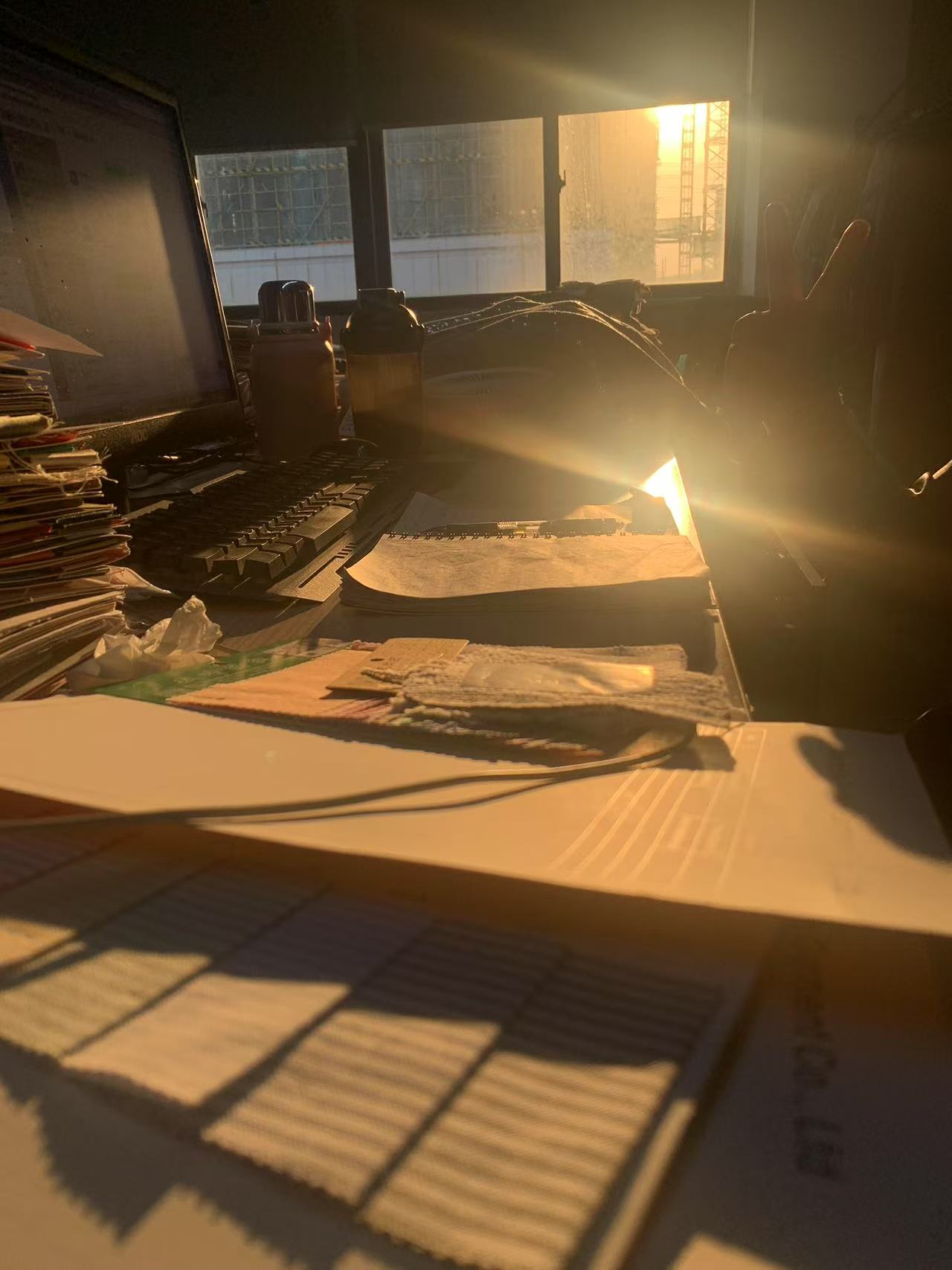
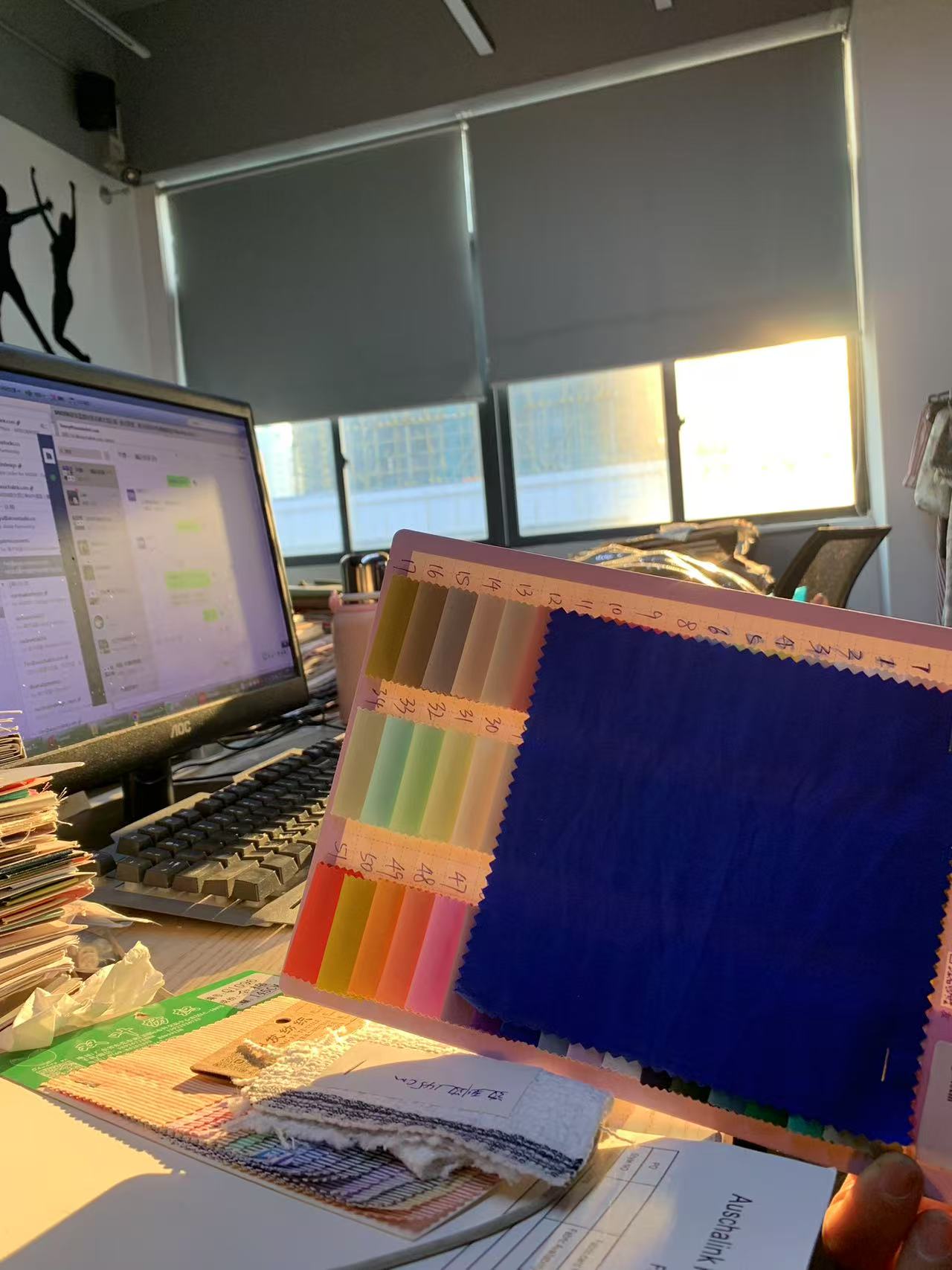
5. Quality Control & Finishing
Completed garments undergo final inspections. Automated scanners detect loose threads or misaligned stitches, while human examiners assess overall appearance. Items are then ironed, tagged, and labeled. For high-end brands, additional steps like hand-embroidery or custom packaging may occur here.
6. Packaging & Distribution
Garments are folded, bagged, and boxed for shipment. RFID tags track inventory in real-time, ensuring timely delivery to retailers or direct-to-consumer hubs. "Our AI-driven logistics system cuts delivery times by 20%," notes supply chain director Kanina.
Sustainability in Focus
The factory has adopted eco-friendly practices, including solar energy, waterless dyeing, and biodegradable packaging. "Consumers demand transparency," says CEO Kanina. "We aim for zero-waste production by 2030."
The Human Element
Despite automation, human expertise remains irreplaceable. "Machines can’t replicate the eye for detail that our tailors bring," emphasizes Kanina. Workers receive ongoing training to adapt to new technologies and safety protocols.
Conclusion
From sketch to store, modern garment manufacturing blends tradition with innovation. As the industry faces pressure to reduce its environmental footprint, factories like Auschalink are pioneering a future where fashion is both fast and responsible.
Post time: Mar-26-2025